Air Compressor Filters
Our compressed air filters are engineered to reduce leaks, blockages, and moisture, ensuring efficient, long-lasting compressor performance.
Lower Operating Costs
The right filter significantly reduces energy consumption and maintenance expenses by efficiently removing contaminants from the air stream.
Enhanced Air Purity
Atlas Copco filters meet the most stringent air purity standards, ensuring optimal performance for your air systems and pneumatic equipment.
Extended Equipment Lifespan
Our cutting-edge filtration solutions prolong the service life of air systems and equipment by preventing contamination-related wear and tear.
How do I find the right air compressor filter for my application?
The first step is to find out which type of contaminant(s) you have to protect your system from and determine the air purity class required for your application.
Identifying the contaminants in your system and determining the required air purity class for your application. Atlas Copco offers a wide range of compressed air filters specifically designed to tackle various threats. Use the table below to select the optimal compressed air filter based on the contaminants present in your system. This ensures your air filtration system operates efficiently and protects your equipment from harmful substances.
Why choose Atlas Copco’s range of air compressor filters?
Atlas Copco’s dedicated filtration team is always looking for ways to give you competitive edge. Our new generation of compressed air filters features several innovations that make your air compressor system more efficient and its operation easier. Here are just three examples:
The ideal filtration technology
To ensure that your system is optimally protected, our filters use different filtration technologies – each designed to take on a specific threat to your airstream. They include:
Wrapped media for wet particles: Wrapped media are known for their durability in wet and oil-contaminated environments. Our patented Nautilus technology combines multiple wrapped layers to offer constant air quality at the lowest pressure drop, even in the harshest working conditions.
Pleated media for solid particles:Pleating is the optimal technology for capturing dry particulates in compressed air. Pleated media have a large surface area and therefore ensure a longer filter service lifetime and lower pressure drop.
Macro-structured activated carbon: Macro-structured activated carbon has a larger surface compared to the typical carbon filter media, giving it a superior adsorption capacity and a steady performance over a longer time.
Cyclone for water: The use of centrifugal forces secures a proper separation of liquid water droplets in the air flow.
To find out more about our filter media and filtration innovations, check out this video
inPASS™ bypass
In addition to outstanding filters, you also get the revolutionary built-in bypass that allows you to service your filter without disrupting the air flow.
To you that means big investment savings by eliminating the need to install an expensive external piping bypass, lower operating and energy costs as well as reduced maintenance times.
Service indicator
To ensure constant air quality, a service indicator allows for an easy check of the filter’s running hours differential pressure, and the maintenance status. It can even send a remote alert.
This table provides information about compressed air filters and their general applications.
Talk to an expert
Choosing the right filter is important and you want to get it right to optimally protect your system and minimize your investment costs. So, if you are still unsure which contaminant you have to filter out or which ISO class you have to meet, just get in touch with Atlas Copco and we will help you find the right solution.
Flanged design
Threaded design
Tower design
Name
|
DDp+
|
PDp+
|
DD+
|
PD+
|
UD+
|
QD+
|
QDT+ |
Grade
|
Rough
|
Fine
|
Rough
|
Fine
|
Ultimate
|
Basic
|
Optimal |
Contaminant
|
Dry dust
|
Oil aerosol/wet dust
|
Oil vapor
|
This table provides information about compressed air filters and their general applications. |
Special applications
Name
|
H
High-pressure
|
SFA
Silicone-free
|
Grade
|
Rough & fine
|
Rough & fine
|
Basic
|
Rough & fine
|
Rough & fine
|
Basic
|
Contaminant |
Dry dust |
Oil aerosol/wet dust |
Oil vapor |
Dry dust |
Oil aerosol/wet dust |
Oil vapor |
This table provides information about compressed air filters and some special applications. |
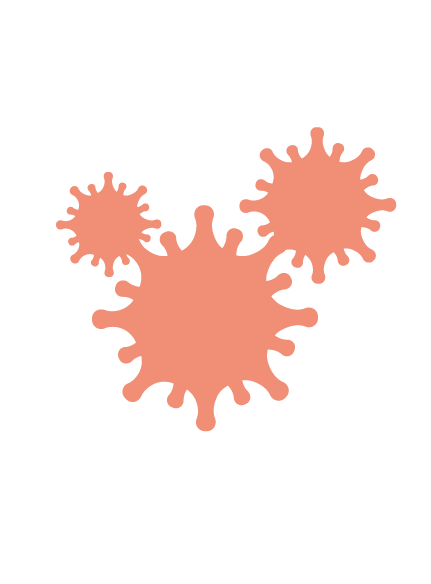
Dry dust

Micro organism

Oil aerosol
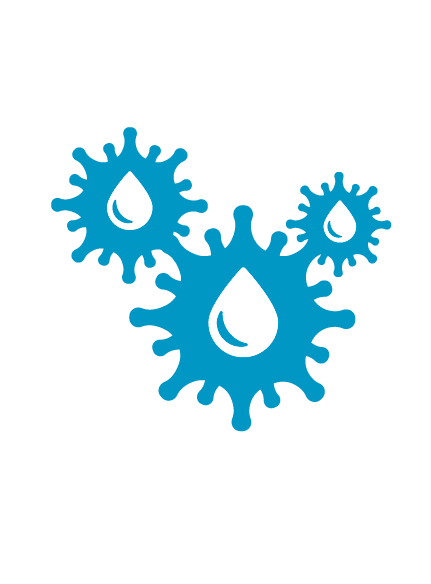
Wet dust
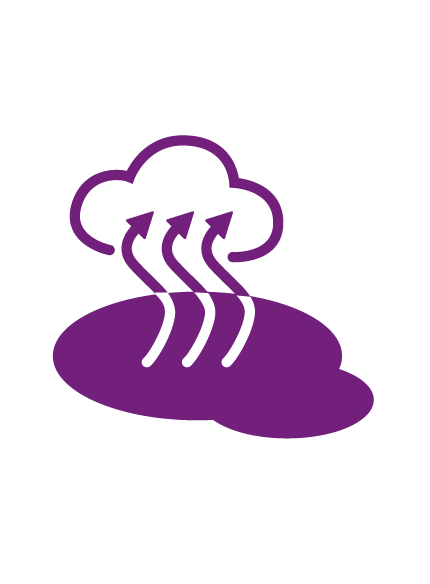
Oil vapor

Water drops
Another way of finding the right filter is to look at your application to determine the air purity it requires according to the international ISO 8573-1:2010 standard. The table below shows the various ISO 8573-1:2010 air purity classes and the Atlas Copco filters and dryer-combinations that meet these classes. To learn more about ISO 8573-1:2010, read our comprehensive blog article on ISO classes for compressed air quality.
ISO 8573-1:2010 class
|
Solid particles
|
Water
|
Oil
(aerosol, liquid, vapor)
|
---|
| Wet conditions
| Dry conditions
| | |
|
As specified by the customer*
|
Oil-free compressor
|
1
|
DD+ & PD+
|
DDp+ & PDp+
|
Desiccant dryer
|
DD+ & PD+
|
& QD+/QDT
|
UD+
|
UD+
|
& QD+/QDT
|
2
|
DD+
|
DDp+
|
Desiccant dryer, rotary drum dryer
|
DD+ & PD+
|
UD+
|
3
|
DD+
|
DDp+
|
Desiccant dryer, membrane dryer, rotary drum dryer
|
DD+
|
4
|
DD+
|
DDp+
|
Membrane dryer, refrigerant dryer
|
DD+
|
5
|
DD+
|
DDp+
|
Membrane dryer, refrigerant dryer
|
-
|
6
|
-
|
-
|
Membrane dryer, refrigerant dryer
|
-
|
*Please contact your Atlas Copco sales representative. |
Examples of typical installations
A |
Compressor - UD+ |
Air purity class ISO 8573-1:2010 [1:-:2] |
B |
Compressor - UD+ - Refrigerant dryer |
Air purity class ISO 8573-1:2010 [1:4:2]* |
C |
Compressor - UD+ - Refrigerant dryer - QDT - DDp+ |
Air purity class ISO 8573-1:2010 [2:4:1] |
D |
Compressor - UD+ - Desiccant dryer - DDp+ |
Air purity class ISO 8573-1:2010 [2:2:2] |
E |
Compressor - UD+ - Desiccant dryer - QDT - DDp+ - PDp+ |
Air purity class ISO 8573-1:2010 [1:2:1] |
*Please contact your Atlas Copco sales representative. |
Related articles
2 February, 2024
Air compressor line filters play a vital role in your compressed air installation. Discover why timely and correct filter cartridge replacement is so important.
Understand the impact of choosing the right filtration media on the efficiency and success of process filtration systems.
10 July, 2023
Coalescing filters are a must when high-quality compressed air is needed. Here is a guide for picking the right one.